In this article, we are going to study what is Valve? and What are different types of valves? in detail.
Note: The PDF file you can download at the end of the articles.
Let’s start our main topic without further delay,
What is Valve?
A valve is a component that controls and regulates the fluid or directs the flow of a fluid by various kinds of closing, opening, or by partially cutting off fluid flow.
So to controls the flow and pressure of fluid within a system, we used valves.
Now our main topic valve types,
What are the different types of Valves?
There are various types of valves for different operations and those are:
- Gate Valve
- Globe Valve
- Check Valve
- Plug valve
- Ball Valve
- Butterfly Valve
- Needle Valve
- Pinch Valve
- Pressure Relief Valve
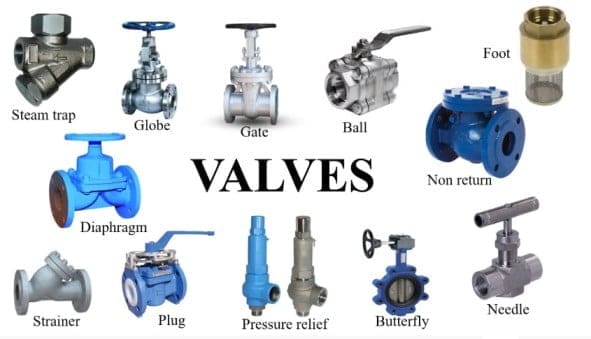
#1. Gate valve:
The gate valve is a regular type valve that is used in any process plant. Here flow of fluid is controlled in linear motion. Gate valves are either in a fully open or fully closed position.
Gate valve is used in nearly all fluid services functioning as air, fuel gas, feedwater, lube oil, steam, hydrocarbon, and close to every system.
It has to provide a good shut-off. It will not be used as a regulating or control valve because when we start to open the gate valves, the passage is slowly opened and Similarly slowly gets closed.
So that a lot of vibration and noise is created at the time of initialization and also the wear of the disc is obtained which causes disc damage which increases the risk of leakage.
So that’s why It will be either in the fully open position or in the fully closed position.
In gate valves, there are different types and those are:
- Solid Wedge Gate
- Flexible Wedge Gate
- Split wedge or Parallel disks Gate
- OS & Y Gate or (Rising Stem) of gate valves
#1.1 Solid Wedge Gate Valve:
The solid wedge disk type is very strong and has very good simplicity so it is very common and widely used in plants. A solid wedge is very much flexible to install in any position. This is appropriate for almost all fluids.
It may also be used in a turbulent flow. It is one of the oldest designs which is still used in various places.
The problem in this is that whenever there is a thermal expansion [Thermal Properties of Material] in this gate, the risk of getting choked increases.
So A solid wedge gate does not reimburse for changes in seat alignment due to thermal expansion or pipe loads.
This kind of disk design is most permitting to overcome the leakage. It is also used in high-temperature service, where a Solid wedge is subjected to thermal locking.
Thermal locking is a situation where a wedge stays between the seats because of the expansion of the metal. These gate valves are generally used in passable to lower pressure-temperature applications.
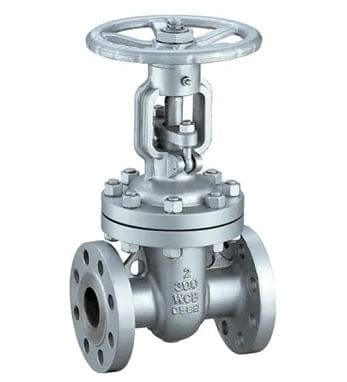
#1.2 Flexible Wedge Gate:
A one-piece solid disk with a cut throughout the perimeter is known as a flexible wedge gate. Its cut dimensions vary in shape, size, and depth. To simplify the problem of the solid wedge, we use a flexible wedge design.
Here we cut Peripheral in the middle of its disc which gives this disk flexibility And whenever there is any thermal expansion, a flexible wedge design will managed.
The problem is that it is not strong like a solid wedge because it has a peripheral cut in it.
For more flexibility, we consider a cast-in recess or wider and deeper cut on wedge perimeter but one of its drawbacks is that it is compromised with strength.
So this design provides better leak tightness and upgrades seat alignment. It also enhances the performance of thermal binding possible.
In steam systems, flexible gate valves are used. There are chances of various distortion in the valves due to thermal expansion of the steam line which causes it to lead to thermal binding.
So as per this problem, we use a flexible gate to overcome the problem of thermal binding.
And one of the disadvantages of flexible gates is that it collects fluid In the disk, which may result in weakening in the disk and corrosion occurs.
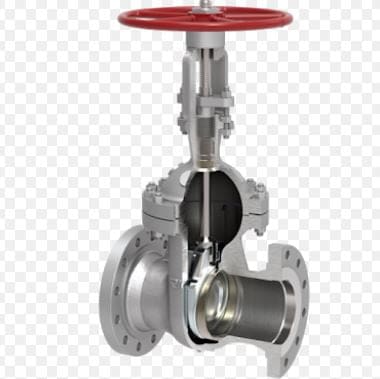
#1.3 Split wedge or Parallel disks Gate:
We use split dishes to fix the problem of both solid disk wedges and flexible wedge gates. So It consists of two disks that connect parallel to each other.
Normally they are spring-loaded and it is always stuck with the seat of the body of the gate, there is also another type of split disk that is parallel in the shape of a disk.
A split wedge disk means it consists of two solid pieces with the help of a special mechanism where both pieces are confined together.
If the disk’s one-half is out of positioning then the disk is free to regulate itself to the seating surface. It may be in a wedge shape or a parallel disk type where parallel disks are spring-loaded which helps in to contact with seats and provides bi-directional sealing.
The split wedge is also used for regulating noncondensing liquids and gasses at normal and high temperatures.
Thermal binding has been prevented through the help of Freedom of movement of the disk. When a line is cold the valves may have been closed. which means it does not create thermal blinding whenever a line is get heated by fluid and expand.
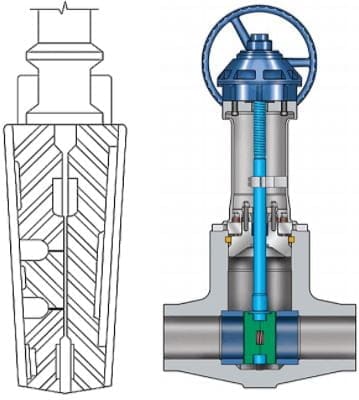
#1.4 OS & Y Gate Valve or (Rising Stem) of Gate valves:
OS & Y are termed as outside stem and yoke or outside screw and yoke. It is one of the valves used to control the flow of water to fire sprinkler systems.
These valves are operated by opening and closing via a gate, and to regulate the lowers into the rises out of valves.
Water allows flowing through the valves when the gate is raised whereas lowering the gate halt the water flowing through the valves.
#2. Globe Valve:
The globe valve is used to start-stop and regulate the fluid in it. Globe stopper occurs at a place in the system where we have to control the fluid flow, and also take into account the leakage and tightness of the system.
It is costlier than gate valves. But it provides good leakproof and tightness than gate valves. Normally the globe valves are used as a control valve.
It is also used for cooling water systems, also used in transport the fuel oil, and lube oil. Its shape is globular at the bottom side that’s why we called it a globe.
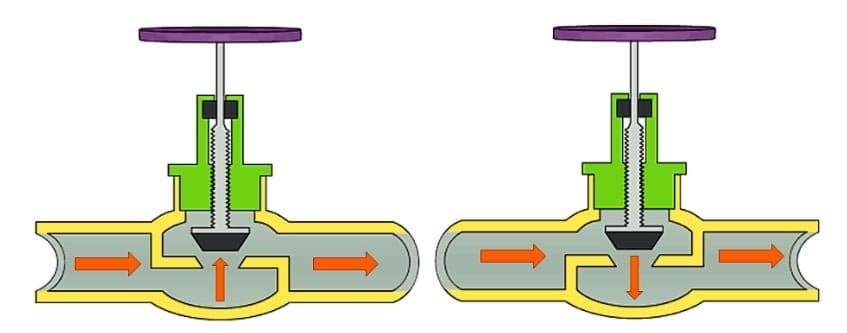
There are three types of Globe valve:
- Z types
- Y types
- Angle types
#2.1 Z types globe:
Z-type globe body is the simplest design of the valve. This globular body contains a Z-shaped partition inside the tap.
The Z-type globular body is designed to consider and simplify the problems in manufacturing, installation, and repair.
These valves do not consider pressure drop but throttling is required.
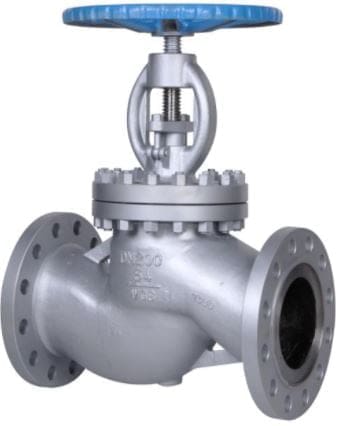
#2.2 Y type globe:
The Y-type valves design are used to solve the high-pressure drop problem in Z-type valves.
So due to simplifying the problem of Z-type, we configure the Y-type, where seats are angled at 45° to the axis of the pipe.
So These valves are used in high pressure and many other reproving services.
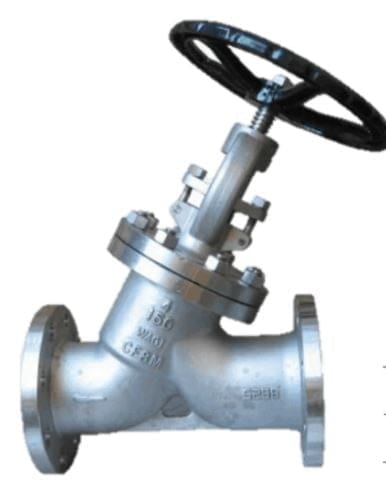
#2.3 Angle types:
These valves are able to turn the flow of fluid direction by 90 degrees without the use of an elbow and extra weld of pipe.
A Disk has open in opposition to the rise and down of the disk. In the case of fluctuating the globe valves have been used, it also competent to operate the slugging effect.
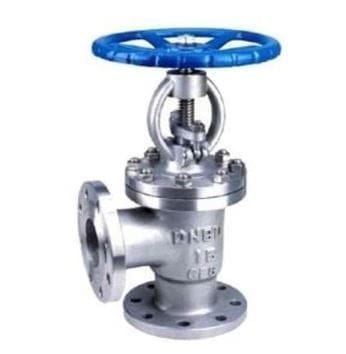
#3. Check valve:
The check valves are used to prevent the backflow in the piping system. check valves allow the flow to pass in one direction.
Whenever back pressure is created in the system, Then the check spigot automatically shuts off And prevents the flow of the fluid.
This is also a nonreturn valve. So the check valves are able to check and intercept the flow of reversal.
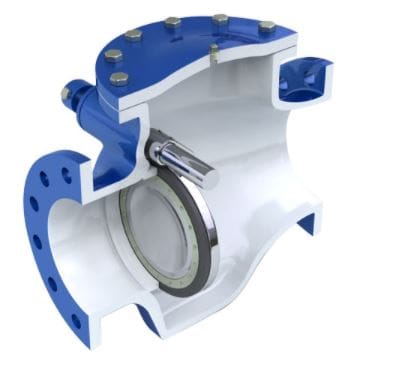
There are three types of Check valves:
- Swing check
- Piston check
- Lift check
#3.1 Swing check:
It is used in low fluid velocities and where flow reversal is not continual. It is used on the discharge side of the pressure relief valves.
#3.2 Lift check:
In this checking device, a disc, piston, and a ball are used for checking in.
A lift check is to be placed in a horizontal or vertical position.
Pressure drops are very high in this system so we used the Lift check plug which is suitable for the small pipeline.
#3.3 Piston check:
It is stem operated and controlled manually or through a motor. These valves are available in various sizes of ranging from 6mm to 600 mm. The construction of material can be cast iron, steel, ductile iron, and corrosion-resistant alloys.
#4. Plug valve:
The plug valve is a quarter-turn rotary valve. In this, the disc rotates in a circular motion and uses valves to open or close.
It is called plug valve because its disc is in the plug shape and it also contains a passage.
It contains leakage of almost negligible. Plug valve has been used in vacuum services, and as can use in high-pressure services and also in high temperature.
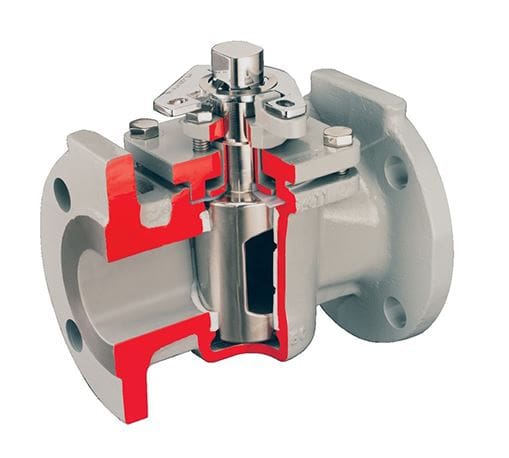
There are four types of Plug valves.
1. Lubricated Plug
2. Non-Lubricated Plug
3. Eccentric Plug, and
4. Expanding Plug.
#4.1 Lubricated Plug:
Lubricated plug valves use a lubricant that mainly consists of a base oil and viscosity improver which is injected to reduce friction and seal ports under pressure between the face of the plug and the seat body.
Lubricant is generally recommended by valves manufacturers for the process fluid, and the resealed occurs in valves after only a few cycles, whereas in some scenarios, it happens after every cycle.
A high maintenance plug valve is used in most operations because it performs very efficiently in applications that have very rare or exceptional operations such as carrying mildly abrasive particle-like gas pipeline systems, dirty upstream applications, etc.
#4.2 Non-Lubricated Plug:
Non-lubricated plug employs a tapered or cone-shape which works as a wedge(chock) and the body cavity presses against a polymeric sleeve.
The sleeve is used to reduce the friction between the body and the plug mechanism.
Non-lubricated plug valves are used where minimum maintenance is required. such as sulfur, hydrogen fluoride, and the liquid where these can be solidified and trapped and potentially jam the valves.
So these valves are limited by the chemical and temperature compatibility of the non-metallic materials they are made of.
There are three types of non-lubricated plug valves:
- Lift-type plug
- Elastomer sleeved plug
- Fully lined plug
#4.3 Eccentric Plug:
The eccentric plug design is advantageous for applications that need a higher seating force and minimal friction from open to close conditions.
The design of plug valves has a half plug used for very wide applications to control the flow such as sewage, sludges and slurries, air, clean and dirty water, and a variety of other services.
#4.4 Expanding Plug:
The expanding plug valve is used to prevent product contamination where double isolation does not require.
It uses various components that help to expand and provides the work of two double blocks has done in one valve.
This valve rotates between the open and closed positions and defends both seals from the flow path.
#5. Ball valve:
The ball valve is Rotary Turn Quarter Valve. It is in the shape of a ball. This is a quick-acting type Which means we can turn off it in 0 or 90 degrees.
The ball spigot is lighter and smaller in size and rating compared to the gate valve.
We control it as we like through the Plunger handle ourselves either clockwise or anticlockwise for on and off the valve.
We used it in the pipeline in domestic houses or in domestic uses of pipes.
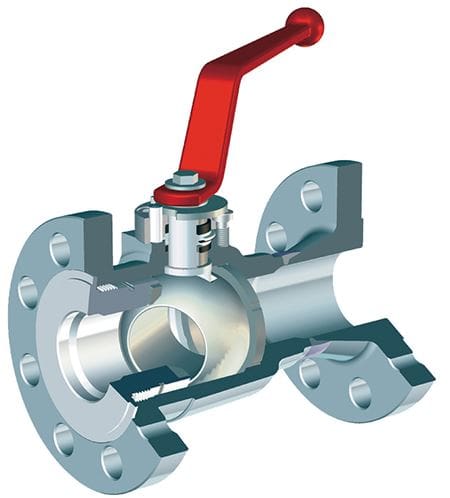
The different Ball valves types:
- Standard
- Hydraulic
- Flanged
- Vented
- Brass ball
- PVC ball and
- stainless steel ball Valve.
#6. Butterfly valve:
The butterfly valve is also a quarter-turn rotary motion valve. It also helps in regulating flow start-stop.
Its biggest benefit is that its body is very thin so it gives it the least space in the piping system, due to this the butterfly valve is used in many applications.
It is very compact and lightweight and it takes considerably less space as compared to other valves.
So it is very easy and fast to open. In this, the disk moves like a butterfly in a closed space.
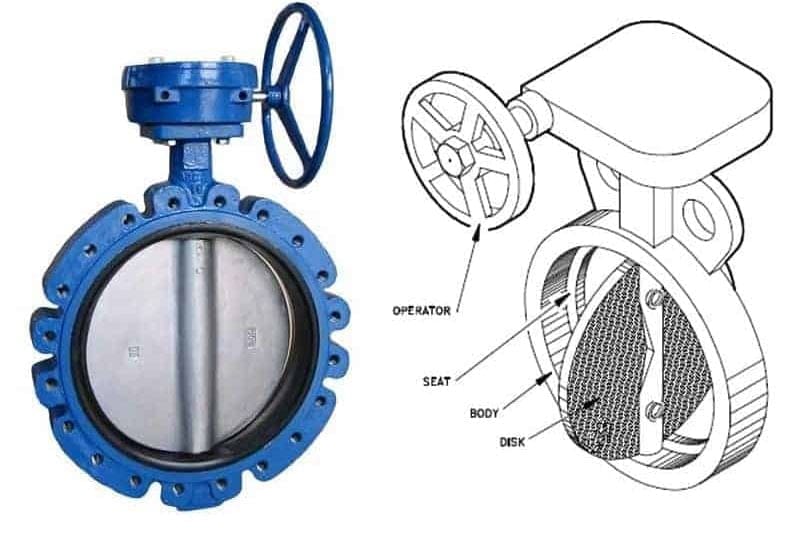
Butterfly valve types:
- Concentric Butterfly
- Eccentric Butterfly
- Wafer Type Butterfly
- Lug Type Butterfly and
- Double Flange Butterfly
#7. Needle valve:
The needle valve design is similar to a globe valve. Its biggest difference is that its disk looks Needle-like pointed.
This is normally used in an instrument where the need for an accurate flow of fluid is necessary.
This is used in a small diameter pipe.
It is very much used in applications where very low pressure can be controlled.
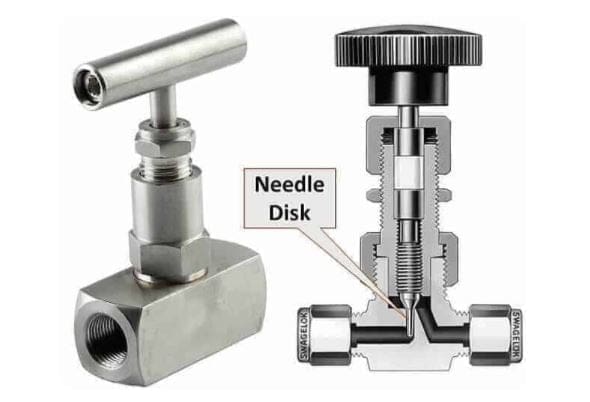
Applications:
It is used in every industry with a wide range of applications such as: for control or metering of steam, oil, gas, water, air, or other non-viscous liquids is required.
#8. Pinch valve:
The pinch valve has a simple mechanism and It has 1 pinch tube. This pinch tube is made of Normally rubber and in this, we can turn the Valve on and off using the pinch mechanism.
Its biggest benefit is that we can use it in a solid particle that has a lot of slurry in it.
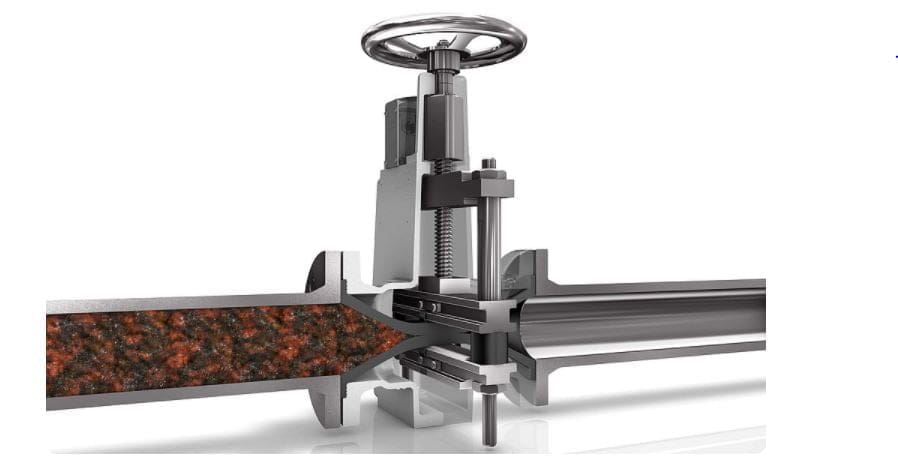
Pinch valve types:
- OM Mechanical Pinch Sleeves.
- OV Mechanical Pinch.
- VM Air Operated Pinch.
- VF Air Operated Pinch.
- VT Air Operated Tanker Pinch.
- VMF Air Operated Pinch.
- VMP Air Operated Pinch.
#9. Pressure relief valve:
The pressure relief releases the pressure whenever an overpressure event occurs in the pressure relief piping system or in the equipment, and the vacuum that is created by it is getting abolished by vacuum valves and protects the piping system.
So the pressure relief secures the piping system.
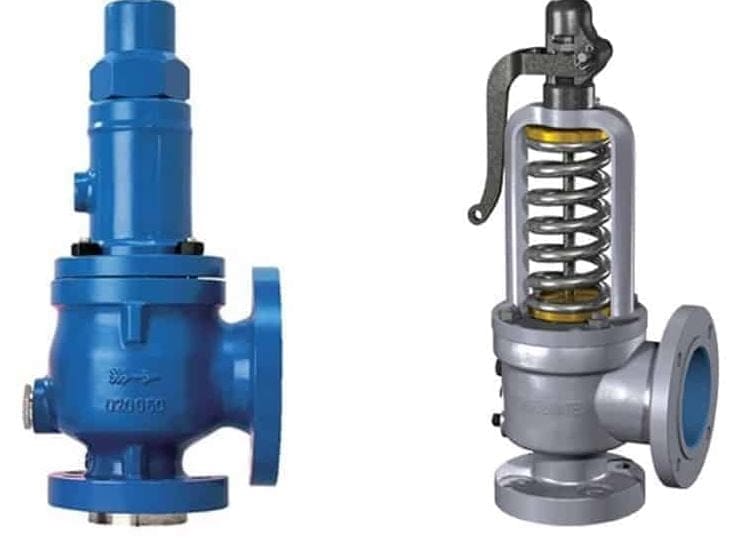
Pressure relief types:
- Spring-loaded pressure relief,
- Balanced Bellows and Balanced Piston valves
- Safety relief
- Pilot operated pressure relief and
- Power actuated pressure relief
Internal Resources for You:
- Gate Valve
- Pump vs Compressor
- Francis Turbine
- Pelton Wheel Turbine
- Types of Fluid Flow
- Impulse Turbine vs Reaction Turbine
- Venturi Meter
- Orifice Meter
Reference [External Links]:
Conclusion:
Here we finally studied all the different types of valves in detail. I hope you have understood this topic in detail. If yes then do not forget to share with your friends and family.
Discussion about this post