In this article, we will study the Definition, Parts or Construction, Working Principles, Advantages, Disadvantages, and application of Abrasive Jet Machining in detail.
At the bottom of every artcile you can downlaod whole document in PDF format.
So let’s start with the definition first,
Abrasive Jet Machining Definition:
Abrasive Jet Machining is a material removal process with the help of concentrated abrasive grains enclosed in a nozzle that removes by the action of impact erosion. In abrasive-jet machining, a high-velocity jet containing abrasive particles is aimed at the workpiece surface under controlled conditions.
The impact of the particles develops a sufficiently concentrated force to perform operations such as cutting, the material is removed by the erosion of work material with abrasive grits at a speed of 150-300m/s. The abrasive grits are carried out in a high-velocity gas stream.
Now coming to construction parts,
Abrasive Jet Machining Parts or Construction:
Abrasive Jet Machining Consists of the following Various Parts:
- Gas Supply
- Filter
- Pressure Gauge
- Mixing Chamber
- Nozzle and
- Abrasive
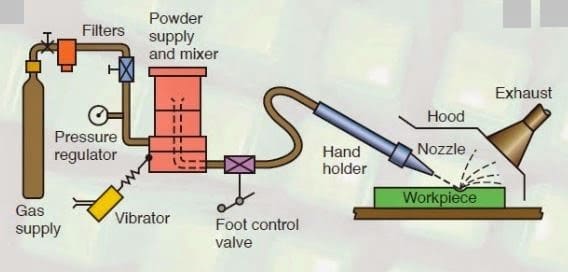
Gas Supply:
A high-velocity jet of airlike nitrogen carbon dioxide etc and enclosed abrasive particles are aimed at the workpiece under controlled conditions. The gas is supplied under a pressure of 2 to 8 kilopascal.
Filter:
The filter is used to clean the fuel supply so that dirt or other impurities do not hamper the progress of the process.
Pressure Gauge:
The pressure gauge is used to control the pressure of the compressed used in the abrasive jet machining. As the pressure decides the depth of cutting and the amount of force required for cutting.
Mixing chamber:
In the mixing chamber abrasive powder is being fed and with the help of a vibrator amount of abrasives can be controlled. So that the abrasives and the gases will be mixed thoroughly in the mixing chamber.
Nozzle:
The nozzle is used to increase the velocity of the fine abrasive jet slurry at the expense of the pressure as we know if we decrease the pressure the velocity will increase. The velocity of the jet will be around 100-300m/s.
The nozzle can be adjusted accordingly so that the desired angular cutting can be achieved and the material will be removed by impact erosion.
The nozzle is usually made up of tungsten carbide because it is subjected to a high degree of wear. The diameter of the nozzle is around 0.2-0.8mm.
The material of the nozzle should be able to withstand corrosion. The nozzle is made of either circular or rectangular cross-sections and the head can be straight or at a right angle.
Abrasives:
Silicon carbide, aluminum oxide glass beads are used as abrasives in abrasive jet machining. The shape of the abrasives can be regular or irregular. The size of the abrasives is around 10 to 50 microns. The mass flow rate of the abrasives is around 2-20 grams/min.
The selection of abrasives depends upon MRR, type of work material, and type of machining accuracy required.
Aluminum oxide (Al2O3) size of 12, 20, 50 microns and it is good for cleaning, cutting, and deburring, Dolomite size of 200 mesh and it is used for Etching and polishing.
Sodium bicarbonate size of 27 microns and used for Cleaning, deburring, and cutting of soft material.
Abrasive Jet Machining Working Principle:
The working principle of abrasive jet machining involves the use of a high-velocity stream of Compressed abrasives particles carried by a high-pressure gas through a nozzle on the workpiece.
Metal will remove due to erosion by the abrasive particles that hit at a very high speed on the workpiece. the pressure energy of the stream is converted into kinetic energy and
Hence the high-velocity jet is produced. The high-velocity abrasive particles remove the material of the workpiece by micro-cutting action as well as a brittle fracture.
The nozzle is made of either circular or rectangular cross-sections and the head can be straight or at a right angle. It is designed that loss of pressure due to the bends, friction, is minimum possible.
The divergence of jet stream increases resulting in more irregular cutting and high inaccuracy.
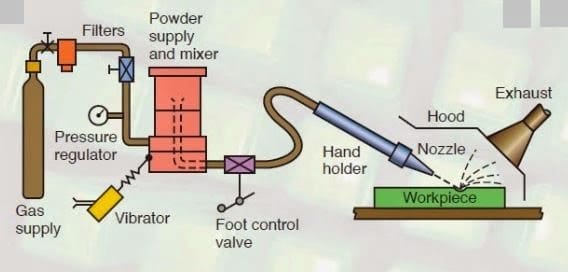
Effect of Grain size and flow rate of abrasives on Material removal rate:
At a particular pressure, MRR increases with an increase in the abrasive flow rate and is decided by the size of the abrasive particles.
But after reaching the optimum value, MRR decreases with a further increase in the abrasive flow rate.
This is due to the fact that the mass flow rate of the gas decreases with an increase of abrasive flow rate and hence mixing ratio increases so that it will do a decrease in material removal rate because of decreasing available energy for erosion.
Effect of exit gas velocity and abrasive particle density:
The velocity of carrier gas carries the abrasive particles changes considerably with the change of abrasive particle density.
The exit velocity of gas can be increased to critical velocity when the internal gas pressure is near twice the pressure at the exit of the nozzle for the abrasive particle density is zero.
If the density of abrasive particles is gradually increased exit velocity will decrease for the same pressure condition.
It is due to the fact that the kinetic energy of the gas is used for moving the abrasive particles.
Effect of mixing ratio on Material removal rate:
As the mass flow rate of abrasive increases its velocity decreases and will thereby decrease the available energy for erosion and ultimately the material removal rate.
Effect of Nozzle Pressure on MRR:
The abrasive flow rate can be increased by increasing the flow rate of the carrier gas. As the internal gas pressure increases abrasive mass flow rate increases and thus MRR increases.
The material removal rate will increase with the increase in gas pressure. The kinetic energy of the abrasive particles is responsible for the removal of material by the erosion process.
Abrasive Jet Machining Working Video:
Abrasive Jet Machining Advantages:
The following advantages of Abrasive Machining are:
- A high surface finish can be obtained.
- The depth of damage is low.
- It provides cool cutting action for glass and ceramics so it can machine delicate and heat-sensitive material.
- The process is free from chatter and vibration as there is no contact between the tool and the workpiece.
- In abrasive jet machining, the capital cost is low as it is easy to operate.
- hard materials(thin section) can be machined like germanium.
- intricate shape holes of brittle materials can be machined.
- The abrasive jet process produces surfaces that have high wear resistance.
Abrasive Jet Machining Disadvantages:
The following disadvantages of Abrasive Machining are:
- Less capacity of the process due to low Material removal rate.
- While machining soft material abrasive gets embedded which will decrease its surface finish.
- The accuracy of cutting is disturbed by the tapering of the hole due to the unavoidable variation of an abrasive jet.
- Accuracy is not good due to stray cutting.
- A dust collection system is a basic requirement to prevent atmospheric pollution and health hazards so the extra cost will be there.
- Nozzle life is limited (300 hours).
- Abrasive powders cannot be reused as the sharp edges are worn and smaller particles can jam the nozzle.
- A small standoff distance can damage the nozzle.
- The process accuracy is poor because of the flaring effect of the abrasive jet.
- Deep holes will have a taper.
- AJM Process is not environment-friendly and causes pollution.
- Airborne abrasives can cause a hazardous atmosphere.
Abrasive Jet Machining Application:
The following application of Abrasive Machining are:
- It is used for abrading and frosting glass, ceramics, and refractories and it is more economical as compared to etching or grinding.
- Cleaning of layering of metals like resistive coating.
- Deflashing small castings and trimming of parting lines of injection molded parts and forgings.
- It is used for engraving registration numbers on toughened glass for car windows.
- AJM is used for cutting thin fragile components like germanium, silicon, quartz, mica, etc.
- abrasive jet machining is used effectively for micro module fabrication.
- Deburring etching, drilling, Cutting, and polishing of hard and brittle materials.
- It can be used for micromachining of brittle materials.
- It is used in fine drilling and aperture drilling for an electronic microscope.
- Used for cleaning metallic molds and cavities.
- Cleaning surfaces from corrosion, paints, glues, and other contaminants.
- Deburring of surgical needles and hydraulic valves, nylon, Teflon, and Delrin.
- Engraving on glass using rubber or metallic masks.
Internal Resources for You:
- Laser Beam Machining
- Ultrasonic Machining
- Electron Beam Welding
- Electrochemical Machining
- Photochemical Machining
- Lathe Machine
- Milling Machine
Reference [External Links]:
- https://www.me.iitb.ac.in/~ramesh/courses/ME338/non_trad.pdf
- https://www.youtube.com/watch?v=EqpdPc7urGQ
- https://www.sciencedirect.com/topics/materials-science/abrasive-jet-machining
This is all about Abrasive Jet Machining notes from my side. Let me know your thoughts in the comment box. If this article helps you then do not forget to share it with your friends and family.
Discussion about this post