Plasma Arc Welding is the advanced version of TIG welding in which high-velocity and coherent plasma are generated which is basically hot ionized gases.
In this article, we will study the Definition, Construction or Main Parts, Working Principle, Advantages, Disadvantages, and Application.
Note: At the end of the article you can download whole document in PDF format.
So lets start with the definition first,
Plasma Arc Welding Definition:
Plasma Arc Welding is a welding process in which arc is generated between a non-consumable tungsten electrode and workpiece by supplying high energy plasma through the ceramic nozzle, it would be combined with an electric arc and produce plasma arc which is having high Kinetic energy and it will be focused at a workpiece at a given point due to this heat concentration on the workpiece will be very high.
Plasma Arc Welding Construction or Main Parts:
Plasma Arc welding consists of following main parts:
- Power Supply
- Welding Torch
- Water Recirculator
- High-frequency unit
- Torch Accessories Kit
- Filler Material and
- Shielding gases
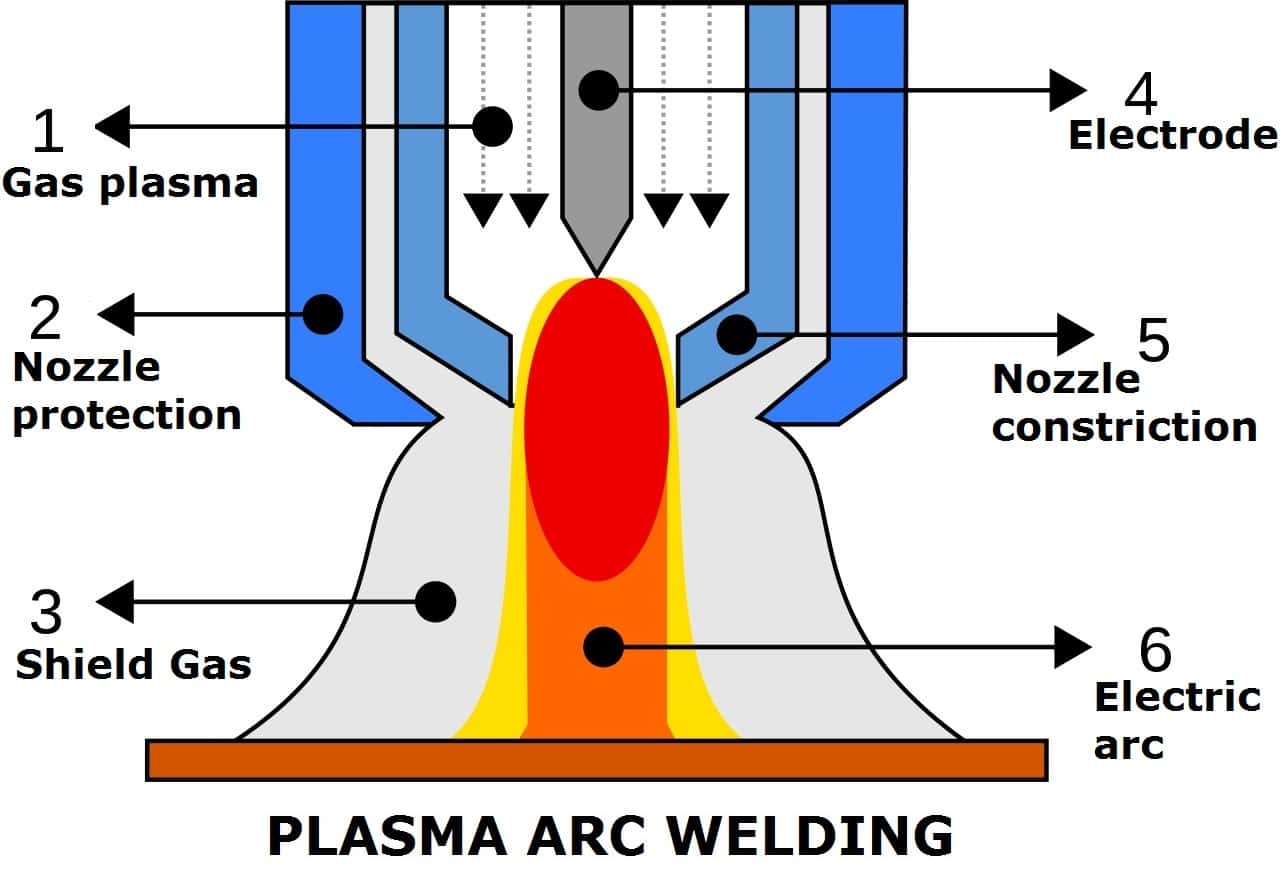
Power supply:
It requires high power dc supply and uses a constant-current type power source. Both Generator and Rectifier types of power sources are used. Tungsten electrode has good electron-emitting capacity therefore it is made cathode because electrons will be emitted from it.
It is also called DCEN polarity. Current can vary from 2-200 ampere and voltage will be around 80 Volts.
Welding torch:
The plasma welding torch consists of non-consumable electrodes, inner nozzle, and an outer gas nozzle uses a water-cooled torch because the very temperature is generated inside the torch. so outside it, a water jacket is provided.
There are two types of DC torches: Non-transferred and transferred.
In non-transferred DC torches, the electrodes are inside the torch. In a transferred torch one electrode is outside, so the arc will form outside of the torch over a larger distance.there is less heat loss in transferred type torch.
Water Recirculator:
The water re circulator is used to circulate the water around the welding torch to cool it because of high-temperature development inside the torch.
High-Frequency Unit:
The plasma arc is not started by a conventional torch start method so an HF unit is used to ignite the spark. so the plasma is made by using 2 cycles:
(a) Producing a very intensity spark also called pilot arc within the torch body by imposing pulses of high voltage, high frequency, and low current
(b) Main current starts flowing between the electrode and the Job and it will lead to the ignition of transferred arc.
Torch Accessories Kit:
These kits are used to improve the performance of welding torch.
Filler Material and Shielding gases:
Shielding used in plasma welding depends upon the type of material to be welded. The filler material used here is the same as that of TIG welding.
Plasma Arc Welding Working Principle:
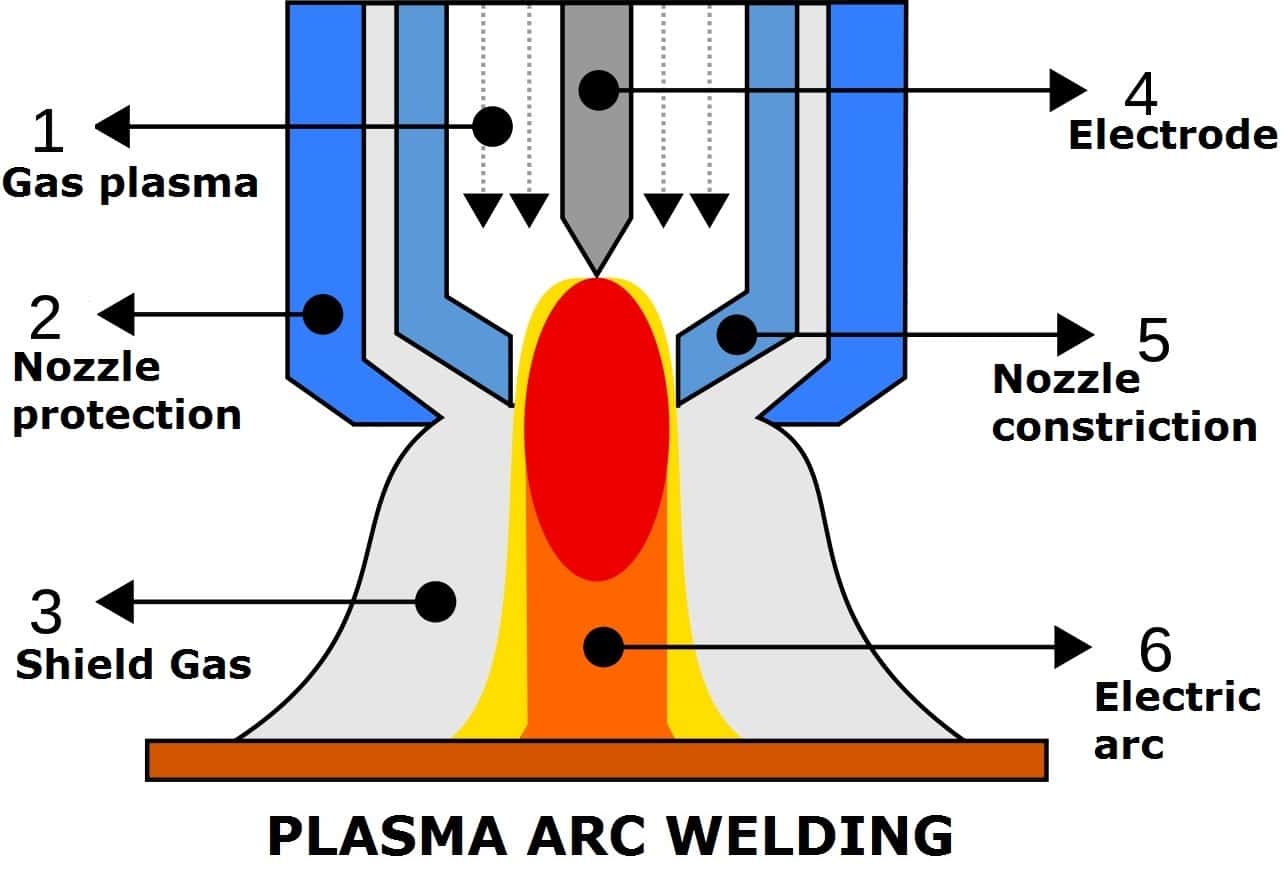
An Arc is set up between a non-consumable tungsten electrode and the workpiece. Charged particles (electrons and ions) formed as a result of ionization of plasma gas tend to reunite when they strike to the surface of the workpiece.
The recombination of charged particles liberates heat which is also used in the melting of base metal. An inert gas is passed through the orifice surrounding the tungsten electrode so the gas will become ionized and conducts electricity. this ionized gas is called plasma.
The plasma is initiated between the tungsten electrode and the workpiece by a low-current pilot arc. The pilot Arc is generally initiated by the use of a High-frequency AC pulse that is superimposed on the main welding current.
After the Initiation of the main Arc, the pilot arc may be extinguished. In the keyhole type plasma welding constriction of arc takes place so the high temperature and the high gas flow results in very high penetration. As the arc moves forward, the material is melted and fills the hole produced due to the force of the arc.
Inert gas is used to protect the molten weld pool from the atmospheric contamination.
Plasma Welding Video:
Following variants of PAW has been developed such as:
- Micro-plasma (< 15 Amperes)
- Melt-in mode (15–400 Amperes) plasma arc and
- Keyhole mode (>400 Amperes) plasma arc
Micro-plasma (< 15 Amperes): Micro-plasma welding systems conditions become good enough to melt thin sheets for plasma welding. because it works with very low plasma current (generally less than 15 A) which in turn results in low energy density and low plasma velocity.
Melt-in mode (15–400 Amperes) plasma arc: Plasma for melt-in mode uses a somewhat higher current and greater plasma velocity than a micro-plasma system for welding. It is generally used up to 2.4 mm thickness sheet
Keyhole mode (>400 Amperes) plasma arc: This type of plasma technique is used for welding thickness more than 2.5mm and normally welding is performed using the key-hole technique.
The keyhole technique uses high current and high-pressure plasma gas to ensure key-hole formation. The high energy density of plasma melts the surfaces of base metal and a high-pressure plasma jet pushes the molten metal developing the key-hole.
Advantages of Plasma Arc Welding:
The following advantages of Plasma Arc Welding are:
- In plasma Arc welding high welding speeds can be obtained
- Penetration is more due to the formation of plasma.
- Higher arc stability is obtained.
- The distance between torch and workpiece does not affect heat concentration on the workpiece.
- The addition of filler material is easier than that of the TIG welding process.
- The thicker jobs can be welded by plasma arc welding.
- A higher depth to width ratio is obtained resulting in less distortion.
Disadvantages of Plasma Arc Welding:
The following disadvantages of Plasma Arc Welding are:
- In Plasma Welding there are higher radiations due to the high-frequency setup.
- Higher Noise (100Db) during welding.
- Plasma arc welding is complicated and requires skilled manpower.
- Gas consumption is high.
- Higher equipment and running costs.
- Higher open circuit voltage requiring higher safety measures to take.
- The narrow width of the PAW weld can be a problem from alignment and fit-up.
Application of Plasma Arc Welding:
The following application of Plasma Arc Welding are:
- The plasma Welding used Piping and tubing of stainless steel and titanium.
- Electric components.
- Submarine Industry.
- Jet Engine Manufacturing.
This is all about Definition, Construction or Parts, Working Principle, Advantages, Disadvantages and Application of Plasma Welding.
Let me know have you understood or not by the use of the comment box. Till then Thank you so much for reading the article and share with your friends too.
Related Article
Laser Beam Machining
Abrasive Jet Machining
Ultrasonic Machining
References [External Links]:
Plasma Welding Overview
Discussion about this post