In this article, I will tell you about the NC (Numeric Control) machine and its construction in detail. In the beginning, you will learn about the definition, construction, Types, and detailed working. Afterward, I will discuss the types, advantages, disadvantages, and applications of the NC machine.
So, let’s get started with what is Numeric Control Machines?
What is NC Machine?
Numerical Control is the machining process that uses a predefined set of alphanumeric code to control the action of the particular tool. These alphanumeric codes contain the information for the movement of the tool.
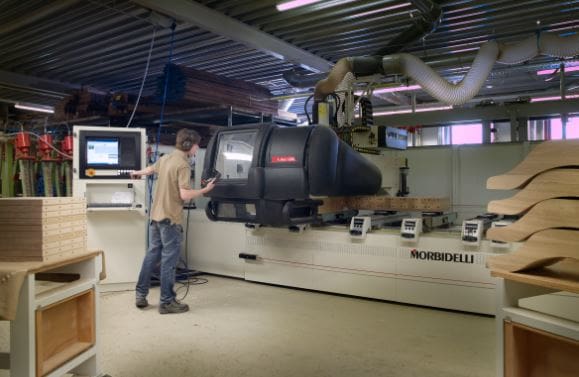
But you might imagine How the NC machine is different from a traditional machine?
In traditional machines, the manual laborers were responsible for controlling different parameters like the speed of a motor, feed rate, direction of rotation, and depth of cut. Whereas, In NC machines, a control panel is responsible for controlling all these parameters.
Did you know? By using numeric control technology now, we can create 3d prints of humans and buildings. Most of the complex to produce equipment or parts are now easy to build due to numeric-control 3d printers.
Parts Involved In Construction of Numeric Control Machine:
The following seven parts involved in the construction of NC Machine:
- Set of instructions or Program
- Machine Control Unit(MCU)
- Signal Output Channel
- Tape Reader
- Data Buffer
- Feedback Channel and
- Machine Tools.
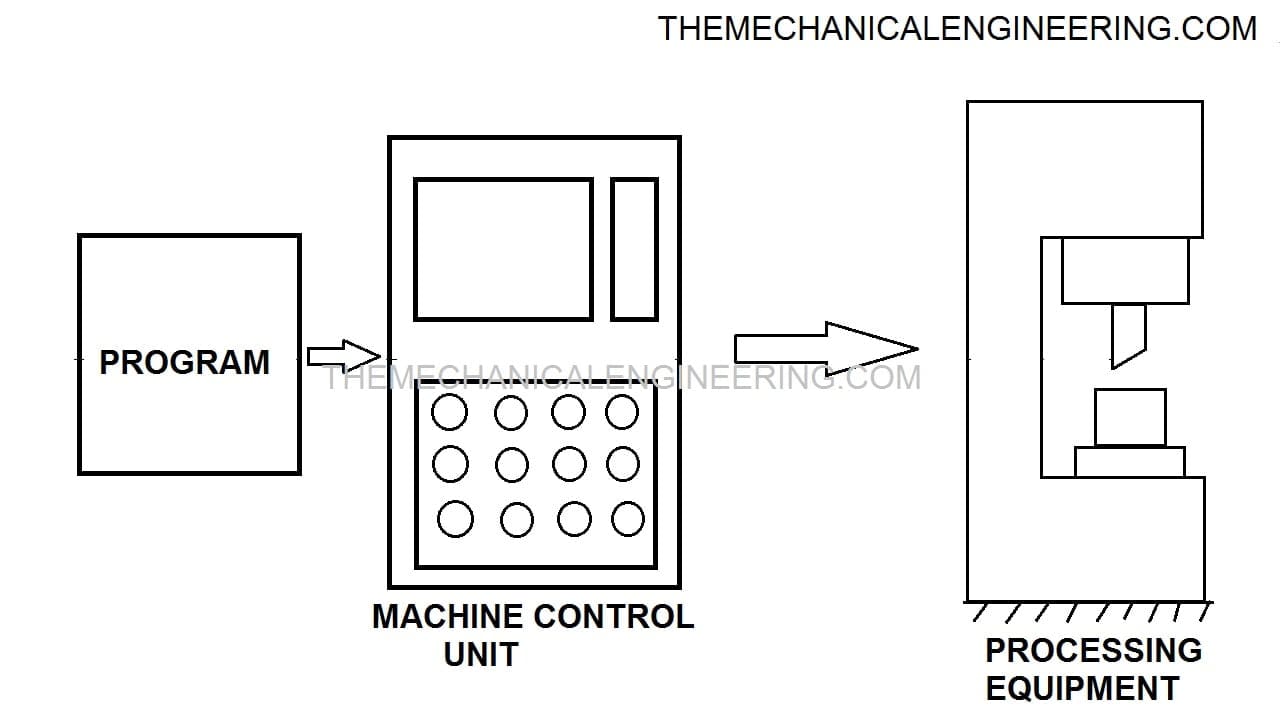
Set of instructions or Program:
A program is the detailed set of instructions that guides the machine tool on what and how to do. The programmer is responsible for writing the program in alphanumeric form. Each step of the program indicates the movement & position of the machine tool. This instruction act as input to the machine control unit (MCU).
To store this set of instructions, we generally use an input medium like L-in wide tape or wide punched tape. Earlier punched cards, 35mm motion picture film & magnetic tapes were used.
Note: There are two other methods of input. The first one is by manual entry of instructions and, the other is by the direct link of the computer, also called DNC (Direct Numeric Control).
Machine Control Unit (MCU):
This part is the brain of a machine. Like, CPU is to the computer. It consists of hardware and electronics which reads and understands the information stored in the input medium and transforms them into action by the machine tool.
Essential components of the control unit consist of a tape reader, a data buffer, a signal output channel, and a feedback channel. Let us understand each one in deep.
Signal Output Channel:
These are responsible for sending instructions to the machine tool(servomotor) about what function to perform and how to perform.
Tape Reader:
It is an electromechanical device that reads the instruction embedded in the punched tape.
Data Buffer:
It reads the data stored in a tape reader.
Feedback Channel:
These are responsible for sending the data back to the machine control unit.
Machine Tools:
It is the part of the machine that performs the function/operation. For example, suppose an NC machine designed to perform machine drilling operations. This NC machine consists of tools like spindles, motors that control movement, cutting tools, work tables, work fixtures, and other supporting equipment.
All these elements work according to the set of instructions from the controller unit. These tools are responsible for performing multiple functions like drilling, cutting, rotation, changing the instruments, etc.
Classification of NC Machine:
The classification of NC Machine has been categorized into four types:
- According to the Motion Control
- According to Control Loops
- Based on Power Supply and
- According to Positioning System.
Lets discuss one by one in detail,
According to the Motion Control:
According to motion control this has been categorized into three types:
- Point to Point Mechanism
- Straight Cut Mechanism and
- Contouring Mechanism.
Point to Point Mechanism:
In this system, the workpiece or spindle moves in the specified position from one point to another so that the spindle can operate on the workpiece. This system is also known as the positioning system. An example is numeric control drilling. It is the simplest of all three methods so, this is the cheapest.
Straight Cut Mechanism:
This system cutting tool is parallel to one of the axes it may be (X, Y, or Z) and moves at a controlled rate. It is suitable for the milling operation to manufacture workpieces of rectangular shape. It can also perform the point-to-point movement.
Contouring Mechanism:
It is one of the most complex and expensive mechanisms as it involves controlling two or more axes at the same time to get the desired shape. In this system, the workpiece moves in a continuous path such that the tool can work while axes are moving, allowing it to produce the angular surface or 2d, 3d curves.
Classification According To Control Loops:
According to control Loops this has been categorized into three types:
- Open Loop and
- Closed-loop.
Open Loop:
In this system, the instructions are given to the motor by the controller but, the movement and the direction are not perfect, but still can generate the desired shape. It is generally cheaper than the closed-loop.
Closed Loop:
This method uses many sensors, transducers, and counters to estimate the position of the table accurately. It uses a feedback unit to compare the workpiece position with the signal received from the controller unit. It is an expensive and complicated system.
Classification Based On Power Supply:
Based on Power Supply this has been categorized into three types:
- Electric
- Hydraulic and
- Pneumatic System
Electric:
This system utilizes AC and DC motors that use the power supply to run. It uses complicated wiring and control systems using circuits.
Hydraulic:
It uses hydraulic pumps and rams to provide the necessary power. It is pretty small in size and has a high torque. It is usually suited for rapid response operations.
Pneumatic System:
This system uses hydraulic rams and pumps. NC machining rarely uses this system because it is large and has low torque.
Classification According to Positioning System:
According to positioning system this has been categorized into three types:
- Incremental and
- Absolute Positioning System.
Incremental Positioning:
In this system, the increment or the change in the previous position becomes the reference point for determining the next position
Absolute Positioning:
In this system, the point of origin is taken as the reference point so, the control unit needs to calculate the position by itself.
NC Machine Working Principle:
The steps to employ the NC machine in the manufacturing process are as follow:
- Planning Process: This process involves the interpretation of engineering drawings of the workpiece according to manufacturing processes. And this planning process is concerned with the preparation of the route sheet. A route sheet is a document showing the series of operations that the workpiece has to go through.
- Programming Process: Under this process, the programmer writes the program according to the sequence of operations the workpiece has to go through or the machining process. The instructions programmed get converted into the output signal that controls actions such as spindle speed, tool selection, tool movement, and cutting fluid flow.
- Tape Preparation: This step involves the punching of the program in the tape. In manual part programming, the program punching is done through the typewriter type device with tape punching ability.
- Tape Inspection: After preparing the tape, the next step comes inspection for checking the accuracy. Sometimes it is performed through the computer program that performs different actions of the tool on the paper. This method can discover the major blunders in tape. And the other way is the “acid test,” which includes performing all the action by the tool on the sample workpiece. This sample workpiece can be made of plastic or foam.
- Production: This is the final step of using the NC tape for production. It includes managing the raw workpiece, specifying and preparing the tooling & any special fixtures, and any other tool required in setting the NC machine for the operation. The NC machine tool loads the raw workpiece and operates on it according to the instruction on the tape. After completing the action raw workpiece, it is unloaded and, another raw material is loaded into the machine.
NC Machine Working Video:
Advantages of NC Machine:
These are the following advantages of NC Machine:
- Reduced Non-Productive Time: NC machine helps in increasing the productive working time of the machine. And helps in reducing the non-productive time by reducing non-productive movements of the machine like changing the tool, workpiece handling time, etc.
- Reduced Time For Completion Of Work: NC machine helps in automating all the manual work like cutting, drilling, etc. So this results in reducing the time required for the completion of work.
- Greater Flexibility: With NC machines it becomes easy to make changes in design, changes in the production schedule, and change over jobs for rush orders.
- Improved Quality: NC machine is used for producing complicated parts where chances for human mistakes are high. It helps in manufacturing parts with higher accuracy, decreased scarp, and lower examination requirements.
- Reduced space requirements: NC machines require less space compared to conventional machines as tools are automated in NC machine so it requires less floor space.
- Can be operated easily: NC machines can be easily operated by less skilled labor. Because all the process in NC machines is automated the labor is required only to monitor the work.
- Avoids Human Errors: NC machines help in avoiding human errors as all the operations are automated and involve the least human interference so, the chances of human errors are the least.
- Results in a reduction of labor cost: The use of this technology results in the reduction of labor cost as it requires the least human interference compared to the conventional machine. So the management can save its cost on labor.
- High dimensional accuracy: Using this technology helps in getting higher dimensional accuracy as compared to the conventional machine.
Disadvantages of NC Machine:
These are the following disadvantages of NC Machine:
- High Investment Required: This system requires higher investment as it has intricate and complex technology. And as it requires more investment so, it requires more aggressive use of the machine by the management to cover its cost by higher production. So that management can bring a greater return on investment.
- Higher maintenance cost: The NC machines use intricate & complex technology and as these are used heavily to recover the investment so, there is considerable wear and tear due to the extensive use so, this machine requires higher maintenance than the conventional machine.
- Involves trained NC personnel: The NC machine needs highly trained personnel as it involves intricate technology that cannot be handled by the normal employee. The problem of finding, hiring, training these employees involves higher costing and time so this is the disadvantage.
- Programming Training required: To make changes in the machine and for troubleshooting the NC machine requires an individual with a deep understanding of NC programming. So, there is a need for programming training for personnel which involves higher costing.
Difference Between Numeric Control (NC) and Computer Numeric Control Machines (CNC):
These are the following differences between of NC and CNC Machine:
- NC stands for Numeric Control whereas CNC stands for Computer Numeric Control.
- NC machine is regulated by the set of instructions that are in form of symbols, numbers and alphabets called the program whereas CNC uses the alphanumeric code to control the motion and movement of tool and workpiece in a more advanced form about manufacturing method and movement.
- NC machine program is stored in the punched tape whereas, the CNC machine program is supplied directly through the computer with the help of a keyboard.
- It is very difficult to make any changes in the program of the NC machine as if we need to make a change in the program of NC we have to feed into the punched tape and then can be executed by the machine but In the CNC machine changes in the program can be made easily as by making the change in the variable the changes can be easily implemented.
- NC machine does not have its storage unit for a program whereas CNC machine has its storage unit.
- To operate the NC machine requires highly skilled labor whereas to operate a CNC machine less skilled labor will work.
- NC machine is less expensive than the CNC machine. And maintenance cost of the NC machine is also less as compared to the CNC machine.
Application of NC Machine:
The NC machines are used in most industries and specifically in metalworking industries. The most common operation in the metalworking industry is metal cutting. In this industry, NC equipment is used for the entire metal removing process (including milling, drilling, and including process like boring, sanding and sawing). It is also used in punch presses and thermal cutting machines.
Steps For Creation of Program For NC Machine:
The person who is programming for the machine must have detailed knowledge about the machine-like parts used in the machine, working of the different tools, functions performed by various components, etc.
- Ascertaining the machining operation to be executed: The first step is to determine the actions the machine needs to perform. It is effortless with simple machines where the steps are less but, in the complex, machines it becomes difficult
- Determining the machine’s action: The order of operation that the tool needs to perform is most important to decide.
- Calculation of coordinates: This step is the most crucial step of the whole process as in this step the programmer needs to do all the computations of the coordinates in which the tool will move. The programmer needs to fix all the coordinates and speed and feed of the instrument. It also needs to set the zero axis and coordinates(x-y-z). Need to determine the depth of the cut, speed of the tool, etc.
- Writing of the program: After gathering all the above information, the programmer writes the program according to the instructions.
Internal Resources:
- Lathe Machine
- Milling Machine
- Drilling Machine
- Planer Machine
- Slotter Machine
- Shaper Machine
- Hot Working Process
- Cold Working Process
Conclusion:
Numeric control machines are an important method of manufacturing that helps the manufacturing industries to produce a different variety of products. There are different types of Numeric control machines like an open-loop, closed-loop, hydraulic, electric, etc.
Hope, So this article has helped you to get a clearer view of the NC machines and their advantages & disadvantages. Make sure to comment on all of your queries regarding the topic.
Discussion about this post