In this article, You will get to know about the hot working process and it’s working in detail. At the beginning of the article, you will learn about the definition, method, and working, then we will be discussing advantages, disadvantages, and applications.
So let’s start with the definition,
What is Hot-working Process?
Hot-working Process is a type of metal forming process and this distinction is based on the particular temperature at which the deformation is carried out. The minimum temperature at which plastically deformed metals form new grains or crystals within a specified time is recrystallization temperature.
Most of the metals have a recrystallization temperature that is one-third or one-half of the melting point of the metal. If the deformation of metal is carried out above the recrystallization temperature.
In other words, we can say that when metal is deformed plastically above the recrystallization temperature but below the burning point it is called the hot working process of metal formation.
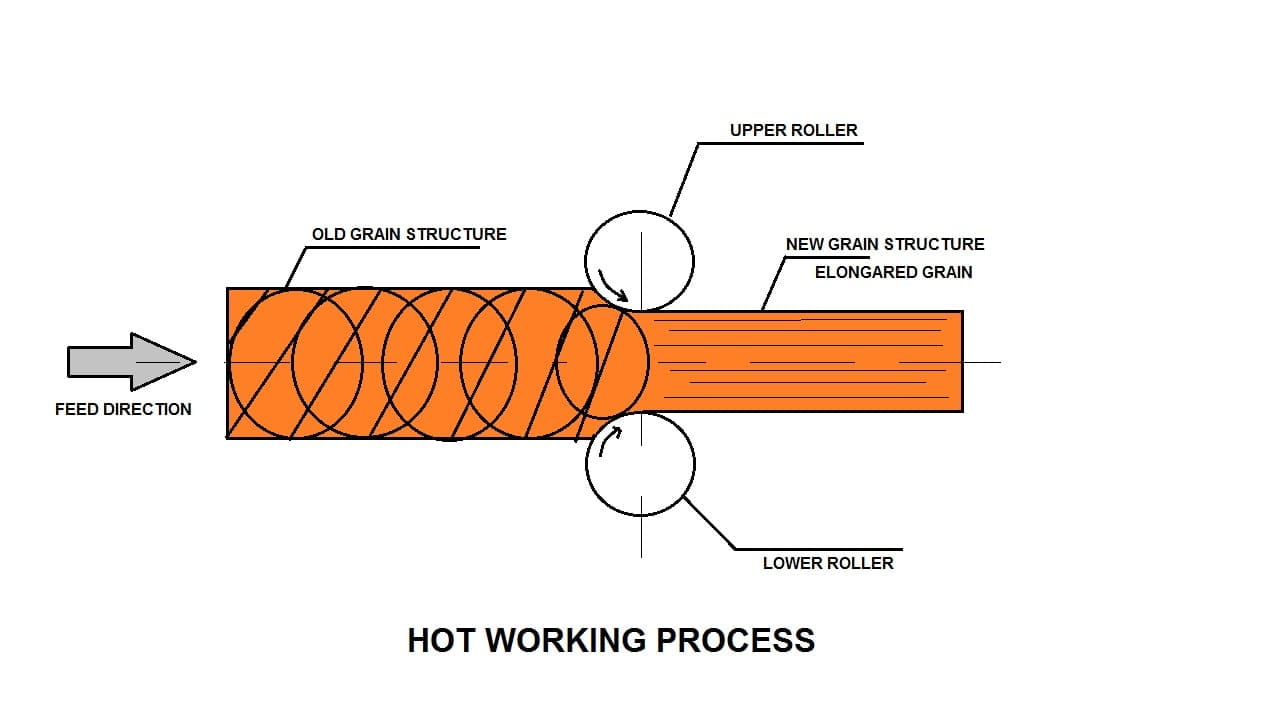
Method of Hot Working Process:
Various Methods of Hot Working Process are follows:
- Hot Rolling
- Hot Forging
- Hot Extrusion
- Hot Piercing Or Rotary Piercing
- Hot Drawing Or Cupping and
- Hot Spinning.
Hot Rolling:
Hot rolling is the process of metal forming in which metal is heated above the recrystallization temperature and then passed through pair of rollers, rolling in the opposite direction but with the same speed to flatten it, lengthen it, and reduce cross-sectional area and obtain uniform thickness.
In other words, we can say hot rolling is the process in which metal is plastically deformed above the recrystallization temperature in the working or rolling operation.
It is commonly used to manufacture metal plates and sheets.
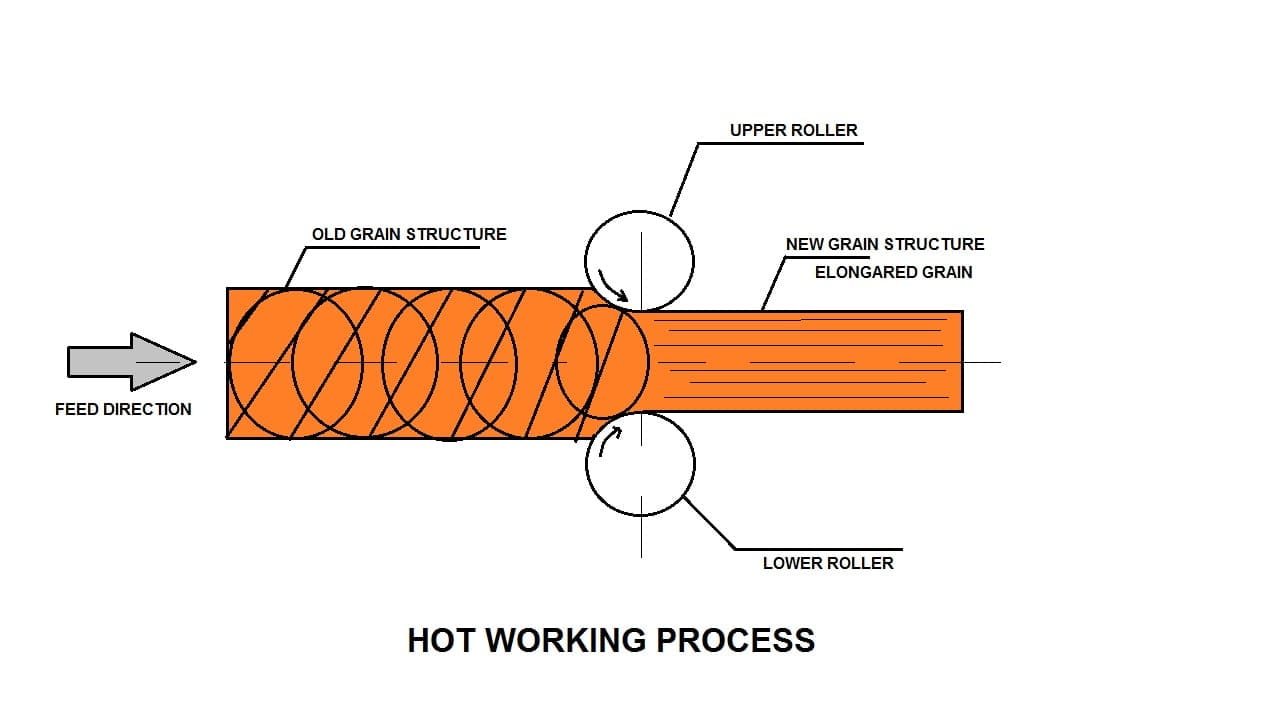
Hot Forging:
This is a very important metalworking process, which is of great commercial importance as it is used by many industries for producing a variety of products.
It is the metal forming manufacturing process involving the shaping of metal through localized compressive forces. It includes heating, deforming, and providing shape to the piece of metal. These localized forces are delivered through a manual hammer or hammer machine and dice.
This hot forging process is useful in manufacturing many industrial components like crane hooks, crank, crankshaft, and wrenches.
Hot Extrusion:
The hot extrusion process is the process of metal forming in which metal is heated above the recrystallization temperature and then pushed through the Die (Manufacturing) of the desired cross-section to convert to the desired shape.
This extrusion process is useful in manufacturing rods, tubes, etc.
Hot Piercing Or Rotary Piercing:
The hot piercing method is also known as the seamless tubing process or roll piercing. It includes rotary piercing to obtain a formed tube by piercing the pointed mandrel through a billet in a specially designed rolling mill.
The solid billet is first centered punched and then heated before piercing. This method is useful in the formation of tubes, pipes, etc.
Hot Drawing Or Cupping:
Hot drawing is the process of metal forming where metal is pulled through a die or set of dies to achieve a material diameter reduction.
In this process, a heated blank of metal is placed on the opening of the die, and punch pushes the blank through the opening of the die to form a cup or shell.
This process is majorly used in the manufacturing of kitchen utensils.
Hot Spinning:
Hot spinning is the process of metal forming where the metal blank is heated to forging temperature and then converted to the desired shape.
The metal is forced to flow over a rotating shape by the pressure of the blunt tool. This method is used to produce the head of refinery equipment and large tanks.
Now moving to working part,
Hot Working Process In Detail:
The process of hot working with metal involves the deformation of a metal at certainly high temperature (above recrystallization point of metal). During this process, recrystallization happens simultaneously with the deformation of the metal.
The phenomena that occur at sufficiently high temperature is called recrystallization, it accelerates the growth of grains in the metal structure, resulting in metal consisting of entirely new grain.
The temperature for hot working of metal depends on the temperature of recrystallization, for example, carbon steel requires a temperature more than 1000 degrees celsius.
Formation of the new grain structure(due to recrystallization) rapidly eliminates the distorted grain structure and strain hardening that is produced due to the deformation of metal during hot working.
50 degrees is the maximum temperature of the metal. Below its melting point. The metal will crumble if the process is done at or near the melting point.
There are various steps for carrying hot working of metal. Firstly the metal is heated to its recrystallization temperature thereafter the intermediate and maximum temperature is fixed to obtain the metal consisting of the maximum number of fine grains.
The finishing temperature is held just above the recrystallization temperature. And the deformation created in the last step is relatively large to maintain fine recrystallized grain size.
Hot Working Process Video:
Hot Working Process Advantages:
The following advantages of Hot Working Process is:
- Hot-working is Suitable for bulk production work.
- The shape and size of metal can be easily changed.
- As the material is above the recrystallization temperature any work can be performed on metal without any stress of hardening.
- As the material is at a high temperature so it has a higher amount of ductility, which means there is no limit on hot-working of metal.
- Due to hot working metals have a refined grain structure. Thus improved mechanical properties.
- Porosity is considerably reduced.
- If there are no errors, hot-work won’t affect strength, hardness, corrosion, etc.
- Higher temperature results in reducing the shear stress, so much less force is required for necessary deformation.
- As the metal is in the plastic state, larger deformation can be accomplished.
- It can improve mechanical, physical & chemical properties.
- This is fast, economic & reliable.
Hot Working Disdvantages:
The following disadvantages of Hot Working Process is:
- Due to oxidation, it leads to a poor surface finish.
- Due to oxidation, there is a loss in carbon sometimes leads to a weaker strength.
- Maintaining and handling the hot working setup is not easy.
- Requires expensive units like a gas furnace or induction heater.
- Dimensional accuracy is difficult to achieve due to the thermal expansion of the metal.
- It is not suitable for all types of metals.
Hot Working Application:
The hot working process is used to manufacture different types of products like tubes, pipes, metal sheets, etc. Different types of products we encounter daily are manufactured using this method like the many types of equipment of automobile, aerospace, architecture, home decor, etc.
Mainly it is used in forging, hot rolling, and extrusion.
Internal Resources:
Forging vs Casting
Cold Working Process
Conclusion:
This is one of the important methods of metal forming that help the manufacturing industries to produce a different variety of products.
There are different methods of hot working process like forging, extrusion, rolling, spinning, drawing, piercing but the most commonly used method is forging & extrusion.
Hope, So this article has helped you. If so then Please Share the article with your friend in need.
Discussion about this post