In this article, we are going to study Different Types of Lubrication System: Advantages and Disadvantages in detail.
You can download PDF format at the end of the article.
What is Lubrication System?
The lubrication system is to provide a sufficient quantity of cooling and filtered oil to give proper lubrication to all the moving parts of an engine. The lubrication systems used for internal combustion engines.
Types of Lubrication System:
There are mainly three types of Lubrication System:
- Mist lubrication system
- Wet sump lubrication system and
- Dry sump lubrication system
Mist Lubrication System:
Mist lubrication system is used in a two-stroke engine, it is not possible to have the lubricating oil in the sump because the charge is compressed in the crankcase. So the mist lubrication is adopted for it.
In two-stroke engines, fuel is mixed with the lubricating oil in the ratio of 3% to 6%. The oil and the fuel mixture are introduced by the carburetor.
The fuel is vaporized and the oil (mist form) goes through the crankcase into the engine cylinder. The mist from oil strikes the crankcase walls, lubricates connecting rod bearings, and the remaining oil lubricates the piston, piston rings, and the cylinder.
The oil mist is generated in the generator by moving the dry air through a venturi. It will make a low-pressure area and the oil will be siphoned from the reservoir.
By this, the oil is added into the high-velocity air stream, and they’re becomes atomized. The oil enters the distribution network because it is an atomized form.
There should be sufficient pressure in the distribution header to impart a velocity to the oil mist. At the oil mist, distribution manifold flow is laminar will be changed to turbulent flow through the distribution channel.
The oil mist is injected into the bearing housing for bearing lubrication and the manifold is used to collect the coalesced oil particles from the drop points.
Mist Lubrication System Advantages:
- Lubrication consumption is very less.
- low cost
- Simple design.
- Bearing life will increase by up to 150%.
- The oil change is not required.
Mist lubrication system Disadvantages:
- The mist lubrication system causes exhaust smoke due to the burning of lubricating oil and forms carbon deposits on the piston crown and exhaust ports which reduces efficiency of the engine.
- The corrosion of the bearing surface because the oil comes in close contact with acidic vapors produced during the combustion process.
- This system requires separate mixing to use of some additive to give the oil good mixing characteristics.this will increase the cost.
- For the vehicle moving down the hill, during closed throttle operation the engine will suffer insufficient lubrication as the supply of fuel is less.
Wet Sump Lubrication System
In the wet sump system, an oil pan is present at the crankcase, sump from which the lubricating oil is pumped to various engine components by a pump.
After lubricating these parts, the oil Bows back to the sump by gravity. It is collected up by a pump and circulated through the engine lubricating system. The strainer is a fine mesh screen that prevents foreign particles from entering the oil circulating systems.
A pressure relief valve is provided which automatically keeps the delivery pressure constant and can be set to High value. When the oil pressure exceeds that for which the valve is set, the valve opens and allows some of the oil to return to the sump thereby relieving the oil pressure in the systems.
Most of the oil from the pump goes directly to the engine bearings and a portion of the oil passes through a cartridge filter which removes the fluid particles from the oil.
This reduces the amount of contamination from carbon dust and other impurities present in the oil. Since all the oil coming from the pump does not pass directly through the filter.
This filtering system is called a bypass filtering system.
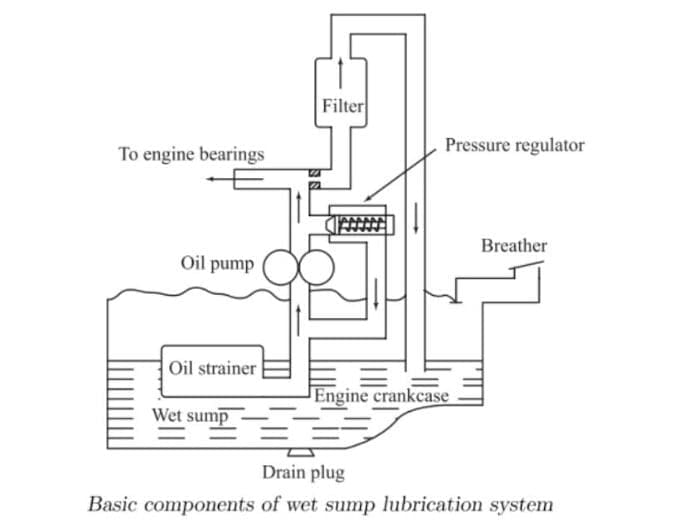
The advantage of Wet sump lubrication system is that clogged filters will not restrict the flow of oil to the engine.
There are three types of the wet-sump lubrication system:
- Splash system
- Splash and pressure system
- Pressure feed system
Splash System:
Light-duty engines use this type of lubrication system. Oil is drawn by a pump delivered, extending the length of the crankcase through distributing pipe into splash troughs which are located under the big end of all the connecting rods.
Maintained at a predetermined level lubricating oil is charged into the bottom of the engine crankcase. Troughs are provided with overflow and the oil in the trowel is at a constant level.
A dipper/splasher is provided under each connecting Rod cap which dips into the oil in the trough on each revolution of the crankshaft and the oil is splashed all over the interior of the crankcase into the pistons and to the portions of the cylinder walls that are exposed.
The oil will pass to the bearing surface and the hole is drilled through the connecting rod cap. To catch the splashing oil over all the main bearings and also over the camshaft bearings to maintained on a pre-determined level.
From the pockets, the oil will reach the bearings surface through a drilled hole.
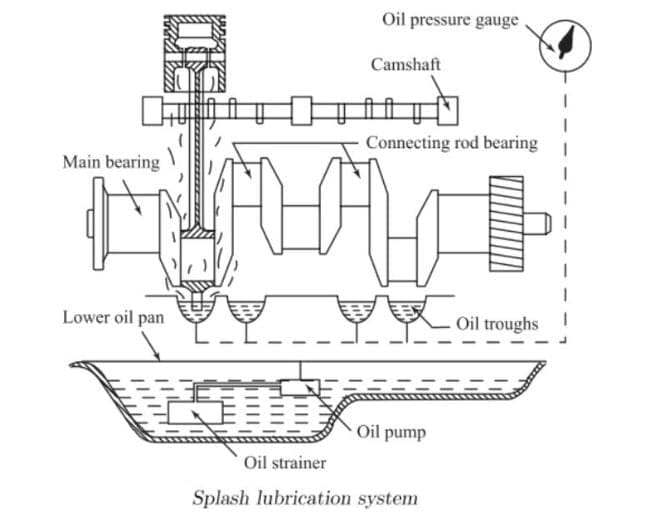
Splash and Pressure Lubrication System:
This system is used where the lubricating oil is pushed under pressure to camshaft bearing.
Also, oil is also supplied under pressure to pipes which direct the oil stream against the dippers on the big end of connecting rod bearing cap, and the crankpin bearings are lubricated by the splash.
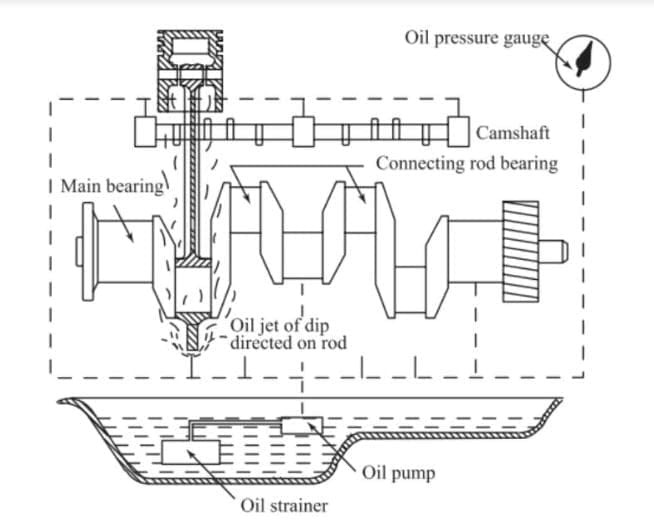
Pressure Feed System:
The pressure feed system is that in which oil is drawn in from the sump and force to all the main bearings of the crankshaft through distribution channels.
The pressure relief valve will also be fitted near the delivery point of the pump which opens when the pressure in the system attains a predetermined value.
Piston pin bearing reached through a hole drilled in the connecting rod. An oil hole is drilled in the crankshaft from crankpin to journal bearing from the main bearings to the crankpin bearing oil that can pass through.
The piston and piston rings cylinder walls, tappet rollers lubricated by oil spray from around the piston pins, and the main and connecting rod bearings.
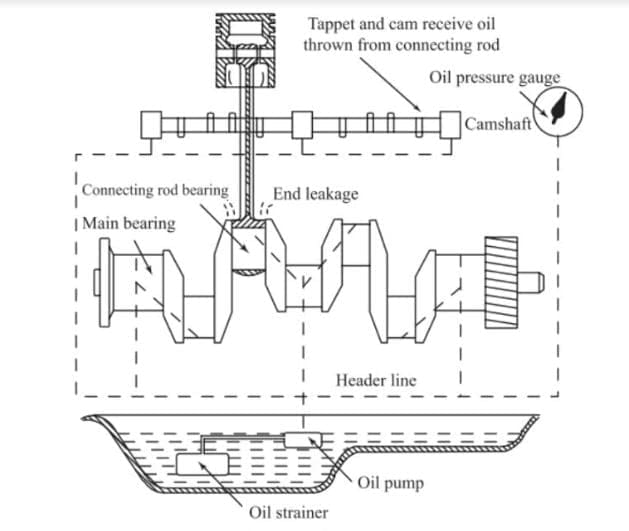
Dry Sump Lubrication System:
A dry sump lubricating system is used for the supply of oil and is carried out in an external tank. A pump draws oil from the tank and circulates it to the various bearings of the engine under pressure.
Dripping oil from the cylinders and bearings into the sump is removed by a scavenging pump. So, oil is prevented from accumulating from the base of the engine.
The capacity of the oil pump is always less than the scavenging pump. A filter with a bypass valve is placed in between the supply tank and scavenge pump in this system.
The pressure relief valve opens permitting oil to by-pass the filter and reaches the supply tank when the filter is clogged.
To remove heat from the oil, separate oil cooler with either water or air as the cooling medium is provided in the dry-sump system.
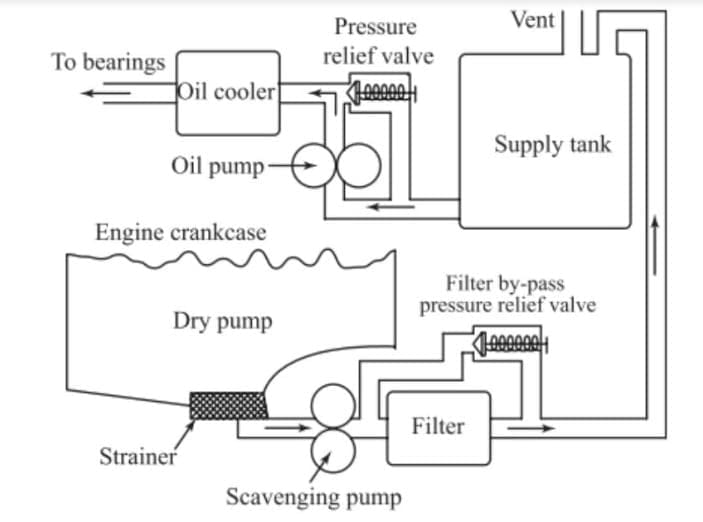
Lubrication System Working Video:
Internal Resources:
Lathe Machine
Milling Machine
Drilling machine
Shaper Machine
Slotter Machine
I hope you liked the article of Lubrication System If so do read another article I have covered. Till then Thank you so much we will meet in other articles.
References [External Links]:
Overview: Google Patent Lubrication
Discussion about this post